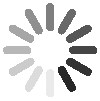
Chương IV: Quy chuẩn kỹ thuật quốc gia QCVN 02:2016/BCT Quy định về an toàn trong thiết kế, chế tạo tời trục mỏ
Số hiệu: | QCVN02:2016/BCT | Loại văn bản: | Quy chuẩn Việt Nam |
Nơi ban hành: | Bộ Công thương | Người ký: | *** |
Ngày ban hành: | Năm 2016 | Ngày hiệu lực: | *** |
Lĩnh vực: | Lĩnh vực khác | Tình trạng: | Còn hiệu lực |
ICS: | *** |
TÓM TẮT VĂN BẢN
Văn bản tiếng việt
Văn bản tiếng anh
1. Thiết kế mới, chế tạo, cải tiến, lựa chọn, lắp đặt trục tải mỏ phải phù hợp với các yêu cầu an toàn đối với tời trục mỏ tại Quy chuẩn này, Quy chuẩn kỹ thuật quốc gia về an toàn khai thác than hầm lò QCVN 01: 2011/BCT, TCVN 4244:2005 và các tiêu chuẩn, quy chuẩn có liên quan.
2. Phải nêu rõ các cơ sở áp dụng tính toán, thiết kế và lựa chọn tời trục mỏ.
3. Vật liệu, chi tiết, linh kiện vật tư phục vụ chế tạo, lắp đặt mới, sửa chữa tời trục mỏ phải:
a) Có đầy đủ mã hiệu, thông số kỹ thuật và phải được tính toán lựa chọn phù hợp với các yêu cầu về kỹ thuật an toàn tại Quy chuẩn này và các quy chuẩn, tiêu chuẩn hiện hành có liên quan hoặc theo tài liệu của nhà chế tạo khi sửa chữa.
b) Phải có chứng nhận chất lượng kèm theo, khi cần thiết phải tiến hành thử nghiệm, kiểm định. Sau khi xác nhận đạt yêu cầu mới được sử dụng.
c) Các chi tiết đúc không có khuyết tật như xốp, có lỗ khí, dị tật, nứt, khuyết thiếu.
d) Các chi tiết rèn không được nứt, tạo tầng, oxit, gấp, sẹo, khuyết thiếu.
e) Các chi tiết hàn với nhau, mối hàn không được nứt, ngậm xỉ, đứt đoạn, cháy.
g) Các chi tiết cạnh sắc, góc nhọn và chỗ lồi cần phải làm cùn phù hợp với tiêu chuẩn hiện hành.
h) Các bộ phận, linh kiện nặng của tời trục phải có vị trí để móc cẩu và treo lên khi lắp đặt.
i) Màu của các bộ phận quay lộ ra ngoài phải được phân biệt với màu của các bộ phận không quay xung quanh.
k) Mỗi điểm tra dầu bôi trơn phải được đánh dấu bằng màu khác với màu của sơn của thiết bị.
4. Thiết bị điện của tời trục phải phù hợp với quy định về an toàn phòng nổ tại QCVN 01: 2011/BCT và bộ Tiêu chuẩn quốc gia TCVN 7079.
5. Khi nhiệt độ môi trường làm việc của hộp giảm tốc nhỏ hơn 8°C phải thiết kế thêm thiết bị gia nhiệt, cao hơn 35°C phải thiết kế thêm thiết bị làm mát.
6. Trong điều kiện làm việc bình thường, tuổi thọ sử dụng của hộp giảm tốc không nhỏ hơn 50.000 giờ làm việc.
a) Nhãn hiệu tời trục mỏ phải phù hợp với quy định tại Nghị định số 89/2006/NĐ-CP ngày 30 tháng 8 năm 2006 của Chính phủ quy định về nhãn hàng hóa.
b) Cách ghi và đọc mã hiệu tời trục mỏ tham khảo Phụ lục II.
1. Số ngày làm việc trong năm đối với tời trục mỏ được tính bằng số ngày làm việc trong năm của mỏ.
2. Khi tính toán thời gian làm việc của tời trục mỏ trong một ngày đêm, cần xem xét đến thời gian kiểm tra trạng thái vỏ giếng, cốt giếng, vị trí đường ống, cáp điện và công tác kiểm tra kỹ thuật an toàn, bảo dưỡng kỹ thuật, kiểm định, hiệu chỉnh định kỳ.
Tổng thời gian trung bình cho các hoạt động này trong một ngày đêm được xác định theo công thức 4:
T = A + B.Hg.10-3, giờ (4)
Trong đó:
Hg - Chiều sâu giếng, m;
A, B - Hệ số được xác định theo Bảng 5.
Bảng 5. Xác định hệ số A, B
Dạng máy nâng |
Số trục tải trong giếng |
A |
B |
(1) |
(2) |
(3) |
(4) |
Tang cuốn cáp |
1 |
2,4 |
2,5 |
2 |
2,6 |
3,0 |
|
3 |
3,0 |
3,2 |
|
Tang ma sát |
1 |
2,6 |
2,6 |
2 |
2,8 |
3,2 |
|
3 |
3,1 |
3,4 |
3. Thời gian tời trục mỏ làm việc trong ngày đêm:
a) Mỏ làm việc 3 ca, tổng số thời gian làm việc mỗi tời trục mỏ giếng chính và giếng phụ theo quy định không lớn hơn 18 giờ trong một ngày đêm.
b) Khi chế độ làm việc 2 ca thì tổng số thời gian làm việc tời trục mỏ giếng chính không lớn hơn 14 giờ, tời trục mỏ giếng phụ 18 giờ.
c) Khi trang bị ba máy trục trong một giếng, tổng số thời gian làm việc không lớn hơn 15 giờ trong một ngày đêm. Nếu chỉ có tời trục mỏ thùng cũi thì tổng số giờ làm việc không được vượt quá 18 giờ.
d) Khi đào sâu thêm giếng, chuẩn bị các tầng khai thác mới, cho phép thời gian làm việc của tời trục đến 20 giờ trong một ngày đêm.
4. Diện tích sử dụng mặt sàn thùng cũi để người đứng cần xác định theo chiều rộng bên trong thùng cũi và theo chiều dài giảm đi 0,4 m. Số người trong mỗi tầng của thùng cũi được xác định trên định mức 0,2 m2 diện tích sử dụng sàn cho một người.
5. Điều kiện làm việc
a) Đối với tời trục mỏ phòng nổ: Theo quy định tại Khoản 4 Điều 17 Quy chuẩn này.
b) Đối với tời trục mỏ không phòng nổ: Không được sử dụng ở những nơi có khí mêtan, bụi than và các thể khí dễ cháy nổ khác.
c) Thích hợp với môi trường lắp đặt: Thiết bị tời trục mỏ phải thích hợp với điều kiện an toàn trong môi trường lắp đặt như: Nhiệt độ, độ ẩm, độ ăn mòn, độ cao.
d) Thiết bị điện trong môi trường ẩm phải đạt tiêu chuẩn IP 54.
e) Thiết bị phải được đặt tại vị trí ổn định, không có rung động mạnh, không có tính ăn mòn.
g) Khi độ cao so với mặt nước biển lớn hơn 1000 m, cần phải nghiên cứu đến tác dụng làm lạnh của không khí và sự giảm của cường độ cách điện, co giãn kết cấu thép. Khi thiết kế, chế tạo, lựa chọn thiết bị phải tính tới yếu tố này.
1. Đối với tời trục mỏ giếng đứng sử dụng máy trục cáp một đầu hoặc máy trục ma sát nhiều cáp.
2. Đối với tời trục giếng nghiêng sử dụng máy trục cáp một đầu.
3. Khi giếng đạt độ sâu lớn nhất và đạt công suất thiết kế, nếu sử dụng máy trục cáp một đầu thì tang quấn cáp phải chứa hết cáp và đảm bảo chuyên chở hết hàng. Trong các trường hợp khác lựa chọn theo tính toán, thiết kế.
4. Cho phép sử dụng máy trục nhiều cáp thay thế cho máy trục cáp một đầu. Trong các điều kiện khó khăn bố trí trên mặt bằng khi xây dựng mỏ nhiều máy trục.
5. Khi chiều sâu giếng lớn hơn 700 m, nên sử dụng máy trục nhiều cáp.
6. Đặc tính máy trục cần chỉ rõ giá trị lực kéo tĩnh lớn nhất và chênh lệch lực căng cáp theo tiêu chuẩn.
1. Tỷ số giữa đường kính tang và đường kính cáp thép
1.1. Đối với máy trục tang trụ một cáp:
a) Đối với máy trục trên mặt đất: ≥ 80.
b) Đối với máy trục dưới hầm lò: ≥ 60.
c) Khi sử dụng cáp thép dạng kín, các giá trị trên phải tăng thêm 20%.
1.2. Đối với máy trục tang ma sát nhiều cáp:
a) Đối với máy trục trên mặt đất (kể cả puy ly tháp giếng): ≥ 90.
b) Đối với máy trục dưới hầm lò: ≥ 80.
c) Khi sử dụng cáp thép dạng kín, các giá trị trên phải tăng thêm 20%.
2. Số lớp cáp cuốn trên tang trụ tời trục cáp một đầu.
2.1. Đối với giếng đứng:
a) Để vận chuyển người hoặc hàng - người chỉ cho phép cuốn 1 lớp.
b) Để vận chuyển vật liệu cho phép cuốn 2 lớp.
2.2. Đối với giếng nghiêng:
a) Để vận chuyển người hoặc hàng - người cho phép cuốn 2 lớp.
b) Để vận chuyển vật liệu cho phép cuốn 3 lớp.
3. Trong thời gian xây dựng giếng để vận chuyển người và vật liệu cho phép quấn 2 lớp.
4. Tang quấn nhiều lớp cáp phải đảm bảo các điều kiện:
a) Vành mép tang phải cao hơn lớp cáp quấn trên cùng ít nhất bằng 2,5 lần đường kính cáp.
b) Đối với ¼ chiều dài vòng cuối của lớp cáp dưới chuyển lên lớp trên phải được tăng cường kiểm tra và luân chuyển theo chu kỳ lắp cáp để thử nghiệm.
c) Tời trục mỏ giếng nghiêng đang hoạt động, khi tiến hành đào tiếp các mức tầng cho phép tăng số lớp quấn lên thêm một lớp khi có cơ cấu để chuyển tiếp trơn tru cáp từ lớp này sang lớp khác nhưng tổng số lớp không được vượt quá 5 lớp.
5. Vành đĩa phanh và tang ma sát phải được tiến hành kiểm tra mối hàn theo Tiêu chuẩn quốc gia TCVN 6008:2010 - Thiết bị chịu áp lực - Mối hàn - Yêu cầu kỹ thuật và phương pháp thử.
6. Tang ma sát và puly dẫn hướng phải được kiểm tra cân bằng tĩnh trước khi xuất xưởng, momen mất cân bằng tĩnh không được vượt quá mô men xoắn của tời trục.
7. Áp suất riêng của cáp lên miếng lót ma sát tang máy trục nhiều cáp không được vượt quá:
a) Đối với cáp kín: 2,5 MPa (25 kG/cm2).
b) Đối với cáp bện dảnh tam giác, cáp bện dảnh tròn, các sợi thép tiếp xúc điểm - đường: Không lớn hơn 2,0 MPa (20 kG/cm2).
c) Giá trị áp suất lớn hơn lấy theo giá trị của nhà chế tạo.
8. Hệ số ma sát m giữa cáp thép và tang dẫn động có lớp bọc phi kim:
a) Đối với cáp kiểu kín: ≥ 0,2.
b) Đối với cáp dảnh tròn và tam giác, tiếp xúc điểm - đường: ≥ 0,25.
9. Đối với máy trục nhiều cáp có thể lựa chọn sơ đồ với góc ôm của cáp trên tang ma sát trong phạm vi 1850 ÷ 1950.
10. Tời trục mỏ với máy trục ma sát nhiều cáp phải được tiến hành tính toán kiểm tra chống trượt cáp.
11. Để giảm lực căng cáp tại các vị trí bắt chặt cáp vào tang, trên bề mặt tang phải còn lại không ít hơn 3 vòng ma sát với lớp lót bằng gỗ hoặc vật liệu tăng ma sát và không ít hơn 5 vòng khi tang không được lót.
12. Tang cuốn cáp
a) Đối với tời trục cáp một đầu 2 tang trụ, có rãnh dẫn cáp, sai lệch chiều dài một vòng tròn tính ở đáy rãnh: Khi đường kính tang D = 2 m ÷ 3,5 m, không lớn hơn 2 mm; khi D = 4 m ÷ 5 m không lớn hơn 3 mm.
b) Độ đảo hướng tâm của tang cuốn phải phù hợp với quy định trong Bảng 6.
c) Độ nhám bề mặt của đĩa phanh, vành phanh Ra ≤ 3,2 mm, sau khi gia công đạt độ chính xác cấp 9.
d) Độ nhám gờ chặn cáp của tang cuốn một lớp Ra ≤ 5 mm, sau khi gia công đạt độ chính xác cấp 8.
Bảng 6: Độ đảo hướng tâm tang cuốn cáp
Đường kính tang cuốn, m |
Độ đảo hướng tâm, mm |
|
Tang cuốn có rãnh cáp |
Tang cuốn dạng lót gỗ |
|
2.0 ÷ 3.5 |
4 |
5 |
4.0 ÷ 5.0 |
5 |
7 |
e) Đối với tang có rãnh dẫn cáp và cuốn từ hai lớp cáp trở lên, phải thiết kế một lớp đệm lót cho rãnh dẫn cáp.
1. Chế độ điều khiển: Điều khiển bằng tay và tự động theo biểu đồ đã lập trình.
2. Dừng tời trục ở chế độ vận hành: Dừng bằng tay và tự động theo biểu đồ đã lập trình.
3. Dừng tời trục ở chế độ sự cố: Dừng bằng tay và tự động.
4. Phần mềm điều khiển tời trục mỏ phải được Việt hóa, đơn vị quản lý vận hành phải có mã khóa mở phần mềm và được hướng dẫn sử dụng.
5. Thiết bị điều khiển, phần cứng và phần mềm điều khiển phải có dự phòng.
Trục chính phải được tiến hành kiểm tra khuyết tật bằng sóng siêu âm. Bên trong trục chính không cho phép có khuyết tật như rỗ và vết nứt, xen lẫn với rạn. Các khuyết tật không được vượt quá yêu cầu như sau:
1. Các khuyết tật tập trung, khuyết tật phân tán, rời rạc trên phạm vi bên trong 2/3 đường kính kể từ tâm trục, phải phù hợp với quy định trong Bảng 7.
Bảng 7: Thông số cho phép khuyết tật trục chính
Tên bộ phận |
Đường kính; mm |
Cho phép tồn tại khuyết tật phân tán |
Cho phép tồn tại khuyết tật tập trung |
Lỗ tiêu chuẩn mẫu để kiểm định, mm |
||
Đường kính lớn nhất, mm |
Số lượng, 100 cm2 |
Đường kính lớn nhất, mm |
Tổng diện tích trên mặt cắt, % |
|||
Trục chính |
≤ Φ 400 |
Φ 6 |
10 |
Φ 4 |
6 |
Φ 3 |
> Φ 400 |
Φ 8 |
10 |
Φ 6 |
8 |
2. Bên ngoài phạm vi 2/3 đường kính từ tâm trục chính, cho phép tồn tại 1 khuyết tật phân tán < Φ 5 ÷ Φ 6 mm chiều dài < 5 mm; cho phép tồn tại khuyết tật tập trung < Φ 4 chiều dài < 4 mm, nhưng diện tích vùng khuyết tật không lớn hơn 5 % diện tích được siêu âm.
3. Đầu trục chính phải đóng dấu số hiệu của trục chính.
1. Vị trí lắp đặt phải an toàn thuận tiện để tiến hành điều chỉnh và thao tác.
2. Duy trì áp suất bằng 1,25 lần áp suất thiết kế trong vòng 5 phút để tiến hành thử nghiệm, kiểm tra sự rò rỉ dầu của toàn bộ hệ thống thủy lực.
3. Trạm thủy lực sử dụng “thiết bị điều áp” với tính năng điều áp phải thỏa mãn các yêu cầu sau:
a) Khi áp suất dầu đạt giá trị Pmax theo thiết kế, dòng điện (điện áp) điều khiển không vượt quá giá trị thiết kế quy định.
b) Áp suất dư P0 (P0 = P - Pmax) phải phù hợp với quy định trong Bảng 8.
Bảng 8: Áp suất dư P0
Áp suất Pmax theo thiết kế |
6.3 |
14 |
21 |
Áp suất P0 |
≤ 0,5 |
≤ 1,0 |
c) Trạm thủy lực của tời trục tự động, khi lắp đặt hai bộ “thiết bị điều áp”, cùng một dòng điện điều khiển I (điện áp U) khi nâng (hoặc hạ), sai lệch về áp suất dầu tương ứng với hai “thiết bị điều áp” khi nâng (hoặc hạ) không được lớn hơn 0,2 Mpa.
d) Trạm thủy lực phải có tính năng điều chỉnh được phanh thứ cấp và thời gian tác động.
e) Trong giếng đứng, khi thùng trục đang di chuyển vào khu vực miệng giếng, chân giếng (vào khu vực giảm tốc) hoặc khi sự cố cho phép bỏ qua phanh sơ cấp, để thực hiện phanh thứ cấp.
4. Khi trạm thủy lực có tính năng phanh sơ cấp, phải thỏa mãn các yêu cầu sau:
a) Khi phanh an toàn: Căn cứ trực tiếp vào sự thay đổi của tín hiệu phản hồi vận tốc, hệ thống áp suất kịp thời điều chỉnh phanh.
b) Thời gian tác động phanh không lớn hơn 0,8 s.
c) Khi phanh sơ cấp không làm việc, phanh thứ cấp phải lập tức tự động làm việc.
5. Trạm thủy lực của tời trục mỏ cáp một đầu hai tang trụ phải thỏa mãn yêu cầu “điều chỉnh cáp”.
6. Trạm thủy lực phải được trang bị áp kế, rơ le áp suất, cảm biến áp suất để thực hiện chức năng kiểm tra, bảo vệ và điều khiển.
7. Trạm thủy lực phải được trang bị cảm biến nhiệt độ dầu thủy lực. Nhiệt độ dầu cao nhất không được vượt quá 70° C.
8. Áp kế của trạm thủy lực phải phù hợp các yêu cầu dưới đây:
a) Cấp chính xác của áp kế không nhỏ hơn 1,5.
b) Phạm vi đo áp suất từ 1,5 ÷ 2 lần áp suất định mức.
c) Khi sử dụng áp kế phải lắp đặt van chặn và thiết bị giảm áp.
d) Áp kế phải được kiểm định theo quy định hiện hành.
9. Trạm thủy lực phải thiết kế bộ phận chỉ báo mức dầu trong thùng dầu, phải đánh dấu mức tối thiểu và tối đa. Bộ phận chỉ báo này phải tháo lắp thuận tiện để bảo dưỡng, sửa chữa.
10. Thùng dầu dạng mở phải lắp đặt bộ lọc sạch không khí; trong đường dầu hồi của hệ thống phải có bộ lọc.
11. Để kịp thời làm sạch và thay thế lõi lọc, bộ lọc phải có bộ chỉ thị ô nhiễm hoặc thiết bị đo.
12. Trạm thủy lực phải có thiết bị điều khiển phanh công tác và phanh an toàn độc lập. Đường dầu điều khiển nhả phanh phải có ít nhất hai đường trở lên và độc lập với đường dầu hồi.
13. Để bảo đảm an toàn, tin cậy, các van phải có liên động với nhau khi tác động.
14. Khi sử dụng máy lọc dầu, lưu lượng định mức phải lớn hơn lưu lượng thực tế của dầu cần lọc.
15. Máy lọc dầu thủy lực phải lọc được tạp chất cỡ hạt 20 mm. Bộ lọc của van phân phối dầu phải lọc được tạp chất cỡ hạt 10 mm.
16. Tạp chất của trạm thủy lực khi dùng lưới lọc 200, không vượt quá 100 mg/m3.
1. Vận hành phải ổn định, không có va đập và chấn động có tính chu kỳ cũng như tiếng động bất thường.
2. Nhiệt tối đa không quá 75° C. Nhiệt độ dầu bôi trơn bên trong không quá 35° C.
3. Độ ồn của hộp giảm tốc không lớn hơn 85 dB (A) đối với tời trục cáp một đầu và không lớn hơn 88 dB (A) đối với trục tải ma sát nhiều cáp.
4. Đầu trục của hộp giảm tốc cũng như chỗ tiếp xúc giữa nắp hộp và thân hộp không được có hiện tượng rò thấm dầu.
5. Độ sạch của dầu bôi trơn hộp giảm tốc thường không lớn hơn 1,8 x A, (mg/m3), độ sạch của dầu bôi trơn hộp giảm tốc hành tinh không lớn hơn 3,4 x A, (mg/m3). A là tổng khoảng cách tâm các cấp của hộp giảm tốc, đơn vị là mm.
6. Tải thử nghiệm phải nhỏ hơn 15% so với tải định mức và thử chạy ngược, xuôi mỗi lần không nhỏ hơn 2 giờ.
7. Trước khi thử nghiệm phải đổ dầu bôi trơn đúng mã hiệu và lượng quy định.
1. Hệ thống thiết bị chỉ báo độ sâu (bao gồm thiết bị chỉ báo độ sâu và bộ truyền động cho thiết bị chỉ báo độ sâu) phải chỉ báo chính xác vị trí của thùng trục trong giếng, đồng thời có thể phát tín hiệu âm thanh, ánh sáng và tín hiệu điện về bàn điều khiển để dừng máy khi xảy ra quá nâng và quá hạ đảm bảo nhanh chóng và chính xác.
2. Sai lệch cho phép về vị trí thực tế của thùng trục so với chỉ báo trong thiết bị chỉ báo độ sâu là ± 50 mm.
3. Mỗi cơ cấu trong hệ thống khi chuyển động phải êm, ổn định, không được có hiện tượng kẹt và sai lệch.
4. Tín hiệu chỉ báo vị trí thùng trục trong giếng phải được thể hiện trên thước chỉ báo độ sâu và trên màn hình tại bàn điều khiển của người điều khiển máy.
1. Tời trục mỏ chở hàng có tổng công suất dẫn động lớn hơn 2500 kW nên trang bị động cơ điện một chiều, đến 2500 kW nên trang bị động cơ dẫn động không đồng bộ với một hoặc hai động cơ, mỗi động cơ công suất 1250 kW.
Để đảm bảo tời hoạt động được liên tục, cần xem xét trang bị động cơ dự phòng.
2. Tời trục mỏ chở người, hàng - người với tổng công suất dẫn động lớn hơn 2000 kW nên trang bị động cơ điện một chiều. Khi công suất đến 1250 kW, tốt nhất là sử dụng hai động cơ dẫn động không đồng bộ.
3. Cung cấp dòng điện một chiều cho động cơ tời trục mỏ phải sử dụng thiết bị nắn dòng đã tiêu chuẩn hóa hoặc sử dụng hệ thống động cơ - máy phát điện một chiều.
4. Xếp loại hộ tiêu thụ điện của tời trục mỏ như sau:
a) Tời trục mỏ chở hàng - người, chở người thuộc hộ tiêu thụ điện loại I.
b) Tời trục mỏ thùng cũi phụ ở giếng gió thuộc hộ tiêu thụ điện loại II.
c) Tời trục mỏ cấp cứu - sửa chữa thuộc hộ tiêu thụ điện loại I.
d) Tời trục mỏ skip để vận chuyển khoáng sản thuộc hộ tiêu thụ điện loại II.
e) Tời trục mỏ skip vận tải đất đá thuộc hộ tiêu thụ điện loại III.
1. Đối với tời trục mỏ skip và tời trục mỏ thùng cũi cần trang bị thiết bị ghi vận tốc theo các thời kỳ của biểu đồ vận tốc. Đối với tời trục mỏ chở người và chở hàng giá trị gia tốc không vượt quá 0,75 m/s2.
2. Vận tốc chuyển động đều của thùng trục trên đoạn hai và sáu của biểu đồ vận tốc bảy thời kỳ không lớn hơn 0,5 m/s. Giảm tốc khi chạm tới vị trí phanh hãm không được vượt quá 0,3 m/s2.
3. Tổng quãng đường chuyển động trên đoạn thứ nhất và thứ hai của biểu đồ vận tốc bảy thời kỳ: Đối với tời trục mỏ skip, bằng chiều dài đường cong dỡ tải cộng thêm 0,5 m; đối với tời trục mỏ thùng cũi - cộng thêm 1,5 m. Tổng quãng đường chuyển động của skip trên đoạn thứ sáu và thứ bảy của biểu đồ vận tốc bảy thời kỳ bằng hai lần chiều dài đường cong, còn đối với thùng cũi - bằng 3 m.
1. Vị trí lắp đặt bàn điều khiển, phải bảo đảm để nhân viên vận hành có thể quan sát rõ ràng được cáp thép, vị trí thùng trục trên thiết bị chỉ báo độ sâu.
2. Toàn bộ phạm vi hành trình của tay phanh, tay điều khiển phải thao tác thuận tiện, linh hoạt, chính xác và tin cậy.
3. Các hệ thống điều khiển tời trục mỏ:
a) Tời trục mỏ chở hàng: Điều khiển được bằng tay hoặc tự động hoàn toàn.
b) Tời trục chở người và hàng - người: Điều khiển bằng tay, tự động trên bàn điều khiển và điều khiển từ xa từ thùng cũi.
4. Vận hành, kiểm tra, sửa chữa giếng đứng và các thiết bị tời trục mỏ, nâng hạ hàng quá khổ, khi sự cố phải đảm bảo khả năng điều khiển bằng tay từ buồng máy.
5. Tại vị trí lắp đặt thiết bị cấp, dỡ tải trên các mức trung gian và các vị trí phục vụ khác phải lắp đặt các nút bấm hoặc công tắc đấu nối với phanh an toàn của máy để có thể vận hành được phanh trong trường hợp cần thiết.
6. Hệ thống tín hiệu bảo vệ an toàn và tác động liên động dừng máy trong các trường hợp tác động bảo vệ do sự cố phải được tự động hóa cao và tin cậy.
7. Mức độ cơ giới hóa và thiết bị phụ trợ
7.1. Thiết kế cần phải đảm bảo cơ giới hóa toàn bộ quá trình cấp, dỡ tải skip và thùng cũi chở hàng (trong chế độ làm việc bình thường), cũng như hoạt động của các thiết bị.
7.2. Tự động hóa hoàn toàn khâu định lượng và cấp tải theo định lượng vào thùng skip.
7.3. Phải sử dụng cơ cấu nối (cầu lật) nối đường ray trong thùng cũi với đường ray ngoài thùng cũi có dẫn động cơ khí và máy đẩy goòng tự động trong các điều kiện an toàn cho phép để trao đổi goòng thùng cũi giếng đứng.
7.4. Tại mức làm việc phía dưới khi chiều sâu giếng lớn hơn 700 m, phải sử dụng tổ hợp cầu lật và cam đẩy.
7.5. Đối với tời trục mỏ giếng nghiêng phải xem xét cam đẩy kiểu bản lề dẫn động cơ khí, bố trí theo đường trục với số lượng tương ứng với số tầng của thùng cũi.
7.6. Phải thiết kế tự động liên động đóng barie cửa giếng và chân giếng. khi thùng cũi, thùng skip và thùng trục rời khỏi cửa giếng và chân giếng.
1. Kích thước nhà, buồng máy tời trục mỏ và dầm chịu lực phải được xác định theo tính toán phù hợp với các tiêu chuẩn xây dựng hiện hành có tính tới yếu tố phục vụ việc lắp đặt, sửa chữa thiết bị tời trục.
2. Khi cáp chạy qua trên tòa nhà bên dưới, phải xây dựng kết cấu chắn để bảo toàn nhà khi cáp bị chùng, võng.
3. Lối đi giữa bàn điều khiển máy và tường không nhỏ hơn 1,5 m, giữa móng máy và tường không nhỏ hơn 0,7 m.
4. Việc bố trí thiết bị tại các nhà lắp máy trục, tháp giếng, bàn điều khiển từ xa có nguy cơ cháy nổ được thực hiện theo QCVN 01: 2011/BCT.
5. Được phép bố trí bình chứa khí nén ở bên trong tháp giếng và các nhà bố trí máy tời trục mỏ.
6. Tại chân giếng và miệng giếng phải có trạm y tế.
7. Nhà đặt thiết bị tời trục mỏ, buồng máy phải đạt yêu cầu tiêu chuẩn Việt Nam hiện hành về môi trường (nhiệt độ, không khí, độ ẩm, độ ồn và rung).
Trong các nhà tời trục mỏ, trên tháp giếng phải tính toán lắp đặt thiết bị nâng hạ để phục vụ sửa chữa, bảo dưỡng thiết bị trong thời kỳ vận hành. Các thiết bị nâng hạ này phải phù hợp với TCVN 4244: 2005. Thiết bị nâng - Thiết kế, chế tạo và kiểm tra kỹ thuật tời trục mỏ.
1. Góc lệch của cáp đối với thiết bị tời trục mỏ giếng đứng và nghiêng (không phụ thuộc vào góc nghiêng của đường lò) ở trên puli định hướng và tang của máy trục một cáp không được vượt quá 1°30'. Đối với tang trụ nón kép, cho phép tăng góc lệch đến 2° về phía trụ nhỏ khi trên bề mặt tang có rãnh.
2. Góc lệch của cáp tại puli định hướng và tang quấn cáp của thiết bị tời trục mỏ giếng nghiêng dưới 30° đang hoạt động không được lớn hơn 2°30'.
3. Khi lắp đặt lại tời trục mỏ một cáp có puli ma sát, các puli định hướng trên tháp phải được đặt trong cùng một mặt phẳng đứng với các puli ma sát.
4. Đối với thiết bị tời trục mỏ giếng đứng, góc nghiêng của cáp so với mặt phẳng nằm ngang không được nhỏ hơn 30° khi chiều dài của cáp trên 45m. Trường hợp đặc biệt, có thể giảm bớt góc đó khi thiết kế đã chứng minh đảm bảo kỹ thuật an toàn khi tời trục mỏ làm việc.
5. Chiều dài của cáp khi không có con lăn đỡ không được lớn hơn 65m. Khi góc nghiêng của cáp so với mặt phẳng nằm ngang lớn hơn 45°, cho phép tăng chiều dài cáp đến 75m.
6. Chiều dài cáp nâng khi không có con lăn đỡ được xác định theo Phụ lục 1, Quy chuẩn này.
7. Khi chiều dài tính toán của cáp lớn hơn quy định tại Phụ lục III cần lắp đặt con lăn đỡ cáp từ giữa nhà đặt máy trục và tháp giếng.
Tình trạng hiệu lực: Còn hiệu lực